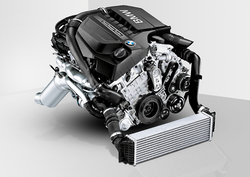
Il turbocompressore sarà sempre più adottato sui motori a combustione interna. Il futuro dei benzina e dei diesel vedrà quindi un impiego massiccio di questa tecnologia.
Il turbocompressore vince sul compressore volumetrico
Come noto esistono due diversi macro sistemi per generare una sovralimentazione di aria: quella che fa uso dei compressori volumetrici, in lingua anglosassone “Supercharging”, e quella che fa ricorso ai turbocompressori, che in inglese viene definita “Turbocharging”.
La prima di queste tecnologie ha trovato larga applicazione sui grossi V-8 americani, mentre sui motori europei, e a dir la verità, di recente, anche su alcuni motori americani, il turbocompressore la sta facendo da padrone. Non è questa la sede per confrontare i due sistemi.
Qui di seguito cerchiamo di capire l’orientamento tecnologico dei costruttori che hanno deciso di impiegare il turbocompressore come sistema per rendere più efficienti i loro motori e, allo stesso tempo, per procedere a passi veloci verso il downsizing.
Come funziona il turbocompressore
Il turbocompressore è una macchina termica che utilizza i gas di scarico per mettere in rotazione la girante di un compressore centrifugo che, a sua volta, si occupa di inviare maggiore aria all’interno dei cilindri.
Il bilancio energetico per l’accoppiamento tra il turbocompressore, che è una macchina fluidodinamica, e il motore alternativo endotermico, che è una macchina alternativa, non è dei più semplici, ma ovviamente è un argomento che a noi non interessa approfondire. Basti sapere che la scelta del turbocompressore corretto è fondamentale per poter ottenere un funzionamento fluido dell’unità a combustione interna.
Un turbocompressore troppo grande manifesterà un ritardo di risposta enorme e il suo beneficio si farà sentire solo ai regimi più elevati. Al contrario, un turbocompressore troppo piccolo genererà una contropressione allo scarico tale da provocare anche una diminuzione delle prestazioni del motore.
Diesel e benzina
L’utilizzo del turbocompressore sui motori a gasolio ha trovato piena applicazione perché il concetto di inviare maggiore aria in aspirazione si sposa perfettamente con un motore che “ingoia” aria e il cui processo di accensione avviene per compressione e non per l’innesco a carico di una scintilla, come invece avviene nel motore a benzina.
È chiaro che con l’avvento dell’iniezione diretta anche sui benzina, l’adozione del turbocompressore è diventata molto interessante anche su questi motori. In precedenza, infatti, i benzina erano tutti pressoché a iniezione indiretta. Il miscelamento tra aria e benzina avveniva quindi nei collettori di aspirazione e in particolare nella loro parte più vicina alle testate. Oggi anche il benzina si ritrova dei condotti di aspirazione liberi da iniettori. Ma non solo. La sofisticata gestione del sistema di distribuzione ha permesso anche, su alcuni motori a benzina, di eliminare il corpo farfallato e quindi le perdite per pompaggio (in realtà il corpo farfallato in molti casi è stato lasciato per questioni di recovery, ma non è più fondamentale per il suo funzionamento).
In altre parole, il ruolo del turbocompressore diventa fondamentale per entrambe le tipologie di motori.
L’efficienza volumetrica nei motori sovralimentati
Perché i motori turbo vantano maggiore potenza specifica? La spiegazione va ricercata nella maggiore quantità di aria che riescono a inviare ai cilindri e quindi, di conseguenza, il maggiore contenuto di ossigeno.
Questo significa poter bruciare più combustibile e/o poter bruciare meglio il combustibile a disposizione. Dal punto di vista strettamente teorico, la massima quantità di aria che un motore aspirato può gestire è pari alla sua cilindrata. Ma questo valore è solo teorico.
Se si tiene conto delle perdite di carico lungo i condotti e, più in generale, delle condizioni reali, come il mancato svuotamento della camera di combustione da parte dei gas combusti, è ovvio che l’efficienza volumetrica intesa banalmente come rapporto tra l’aria realmente aspirata e quella teorica, non sarà mai pari a 100, ma, quando va bene, può superare il 70% ed eventualmente arrivare all’80%.
Con il turbo tutto cambia, perché l’aria viene forzata a entrare grazie all’energia che gli viene impressa dalla girante del compressore centrifugo.
Le difficoltà iniziali seguite dal successo
La sfida tecnologica, ossia la realizzazione delle diverse parti che compongono il turbocompressore, ha rappresentato sicuramente uno dei limiti allo sviluppo.
A questo tipo di problema vanno aggiunte la difficoltà di gestione della modulazione delle pressioni di sovralimentazione e l’impiego di materiali sufficientemente resistenti al carico meccanico e a quello termico, che tra l’altro vengono esercitati sempre in contemporanea tra loro.
In più, come anticipato a inizio articolo, una delle sfide più importanti è stata rappresentata dal problema di accoppiamento tra due macchine termiche molto differenti tra loro, tanto che l’adozione planetaria che stiamo conoscendo ai nostri giorni è stata possibile anche grazie all’adozione di tecniche particolari nella realizzazione dei vani di ingresso delle turbine, sdoppiandoli o nei casi più sofisticati impiegando la nota geometria variabile.
Di cosa si tratta in questo caso è presto detto. L’accelerazione dei gas in ingresso alla parte calda del gruppo di sovralimentazione, quindi alla turbina, è funzione della quantità dei gas stessi e delle sezioni di passaggio lasciate a loro disposizione. Con un flusso basso è auspicabile infatti avere piccole sezioni, mentre in corrispondenza delle portate più alte è bene avere sezioni maggiori. Questo viene ottenuto con delle palette orientabili legate alla parte fissa dell’ingresso in turbina. Orientando le palette, infatti, è possibile creare delle zone con sezione di dimensione differente.
Le mappe e la loro interpretazione
Ogni turbocompressore viene identificato dalle mappe di funzionamento di turbina e compressore. Queste mappe sono appannaggio dei tecnici che si occupano di progettare il motore e di cercare il gruppo di sovralimentazione più adatto.
Vale però la pena capire, anche solo dal punto di vista strettamente teorico, il principio che regge la loro interpretazione.
Il funzionamento del compressore viene sintetizzato attraverso alcune curve che concorrono a formare delle mappe di esercizio all'interno delle quali è possibile identificare le condizioni di massima efficienza.
Queste mappe portano sull'asse delle ordinate il rapporto di pressione e sulle ascisse la portata in massa o in volume di aria. Le linee che delimitano le condizioni ideali di funzionamento di un compressore centrifugo sono definite “linee di choke” e “linee di surge”.
La “choke line”, o linea di soffocamento, è la linea che si trova alla destra della mappa di funzionamento del compressore e rappresenta la condizione in cui il flusso all'ingresso del compressore raggiunge la velocità sonica. In queste condizioni non è possibile ottenere alcun incremento ulteriore del flusso.
La “surge line”, o linea di rigurgito, è la linea all'estrema sinistra della mappa e rappresenta la condizione di stallo per il flusso d'aria in corrispondenza dell'ingresso nel compressore. Quando la pressione è troppo alta e il flusso è troppo basso, il fluido, cioè l'aria, non aderisce più bene alle pareti aspiranti delle palette del compressore, a tal punto che il flusso si interrompe. A questo punto il flusso all'interno del compressore si inverte, finché non si stabilisce un rapporto di pressione idoneo e il flusso riprende in direzione corretta. Questo fenomeno si ripete ciclicamente e l'instabilità fluidodinamica lavora a una frequenza propria. Il rumore che si percepisce è noto appunto come fenomeno di “surging".
Per completare il quadro, ricordiamo che il compressore centrifugo è il lato freddo del gruppo. Si compone di una chiocciola e di una girante e il suo compito è quello di inviare aria in pressione in camera di combustione. L'aria in arrivo dal circuito di aspirazione entra assialmente nella chiocciola ed esce radialmente spinta dalla girante. La turbina, invece, rappresenta il lato freddo del gruppo di sovralimentazione e si compone, come il compressore, di una girante e di una chiocciola. In questo caso, però, il flusso dei gas in uscita dal motore prevede un ingresso radiale e un'uscita assiale.
L’attuale impiego del turbocompressore e i gli indirizzi futuri
I motori a gasolio senza turbocompressore praticamente non esistono più, almeno nel settore del trasporto turistico. Se consideriamo i benzina, invece, qualche aspirato lo troviamo ancora, ma anche per loro il turbo sta diventando sempre più importante.
Tanto per citare un esempio, ricordiamo il percorso scelto da Ford con la propria famiglia di motori EcoBoost, che si sta allargando a macchi d’olio all’interno della gamma di questo costruttore.
Il tre cilindri di 1.0 litri che sta equipaggiando la Fiesta e altre auto del gruppo, è stato motore dell’anno per più volte, ma la casa americana non è certo l’unica ad aver intrapreso questo percorso di downsizing. Si pensi a Volkswagen, a Mercedes, a BMW, ai francesi di Renault, Peugeot e Citroën, tanto per citare solo alcuni esempi.
Ora, partendo dal presupposto fondamentale secondo cui un turbocompressore troppo grosso fornisce seri ritardi di risposta e poca gradualità di funzionamento, mentre un turbo troppo piccolo genera problemi di contropressione allo scarico in corrispondenza delle portate più elevate, è evidente che il futuro della sovralimentazione mediante turbocompressore si gioca tutto sulla possibilità di realizzare gruppi poliedrici capaci di adattarsi alle differenti situazioni di funzionamento.
La geometria variabile
Come molti già sapranno, il lato caldo del turbocompressore è costituito dalla turbina e dalla sua chiocciola. I gas che arrivano dal motore entrano radialmente in turbina ed escono assialmente. A governare il tutto sono le complesse leggi della termofluidodinamica.
Per semplificare il discorso, però, possiamo pensare di legare il flusso in ingresso alla turbina alla sezione della turbina stessa. Quando i flussi di massa sono molto bassi, è evidente che servirebbe avere a disposizione sezioni piccole e turbine particolarmente leggere, con bassa inerzia. Questo consentirebbe di avere un’ottima accelerazione del gruppo di sovralimentazione e quindi una risposta immediata alle richieste del conducente. La situazione opposta porta a un ritardo di risposta che si traduce in una guida poco fluida in cui accelerazioni forti vengono impresse per brevi periodi. In tutti gli altri campi di funzionamento, invece, il motore appare fiacco. Questo è il motivo che ha portato all’introduzione della geometria variabile, che sui benzina ha sempre rappresentato un grosso problema, proprio in virtù delle temperature più elevate dei gas di scarico.
I costruttori hanno messo in campo diverse soluzioni, tra cui l’adozione di materiali avanzati per realizzare una geometria variabile simile a quella dei motori a gasolio o la soluzione nota anche come “twin scroll”. Quest’ultima prevede due sezioni di ingresso differenti in turbina, in modo tale da ottimizzare il flusso a seconda del regime di giri del motore. Ne rappresenta un esempio tipico il motore M133 di 2.0 litri di Mercedes-AMG.
Il doppio e il triplo turbo
Molto probabilmente BMW può essere considerata pioniera della motorizzazione moderna di massa che ricorre all’utilizzo di più gruppi di sovralimentazione.
Il concetto che sta alla base di questa soluzione è quanto mai semplice: utilizzare turbocompressori piccoli in corrispondenza delle portate più basse e turbocompressori grandi per i flussi più elevati. Nel caso di richiesta di massima potenza si può anche prevedere l’utilizzo contemporaneo di entrambi i turbo.
Il problema della moltiplicazione dei gruppi di sovralimentazione pone questioni di bilanciamento dell’energia ancora più complicati. Bisogna infatti sempre tenere a mente che, nel bilancio totale, l’energia assorbita non dovrà mai superare quella resa disponibile. Se così fosse, infatti, invece che aumentare la potenza specifica del motore ne otterremmo una diminuzione. Ma non solo. Accoppiare un motore con uno o più gruppi di sovralimentazione richiede una pianificazione dei layout, layout tra loro anche molto differenti.
I turbo, infatti, possono essere posti in serie e/o in parallelo. Nel caso dei turbo in serie, il flusso attraverserebbe prima uno e poi l’altro gruppo. Nel caso di gruppi in parallelo possono essere fatti funzionare i due turbocompressori in tempi diversi o contemporaneamente.
In realtà anche con i gruppi in serie si possono ottenere dei funzionamenti particolarmente complessi escludendo un turbo o l’altro a seconda di come il circuito viene pensato, anche utilizzando della valvole di esclusione o di ricircolo.
È inutile fare degli esempi specifici, ma se sfogliate il listino BMW scoprirete come il costruttore di Monaco abbia messo in commercio soluzioni con un solo turbo (tradizionale), con due turbo e anche con tre turbocompressori. Stiamo parlando di motori super complessi, con potenze specifiche elevatissime e con dei costi di manutenzione non sempre così abbordabili. Ma il futuro vedrà un impiego sempre più massiccio della sovralimentazione.
L’assistenza elettrica
Anche in questo caso ci troviamo di fronte a una tecnologia in divenire. Poter fornire un’assistenza elettrica al gruppo di sovralimentazione è sicuramente un’ottima idea, soprattutto per quelle situazioni in cui l’inerzia della turbina o la bassa portata dei gas renderebbero un turbo lag (ritardo di risposta troppo elevato).
Gli esperimenti fatti sino ad ora mettono in evidenza un assorbimento eccessivo di energia da parte dei motori elettrici e alcuni test che sono stati effettuati da Audi hanno anche portato alla luce i limiti degli attuali impianti elettrici a 12 Volt.
Per mettere in campo l’assistenza elettrica nella produzione di serie, si dovranno modificare i layout degli impianti elettrici e bisognerà cercare di diminuire gli assorbimenti energetici da parte dei motori che dovrebbero fornire l’assistenza elettrica. Una delle idee attualmente considerate prevede la costruzione di condensatori capaci di accumulare energia dai gas caldi, energia che successivamente verrebbe restituita per il funzionamento del motore elettrico.
Ci troviamo di fronte a un caso complicato di bilanciamento energetico, ma nel futuro potremmo vedere sicuramente l’applicazione di questa tecnologia.
L’iniezione di acqua in aspirazione
Citiamo questo tipo di tecnologia per dimostrare quanto lontano si stiano spingendo i costruttori. Un esempio per tutti è proprio la BMW M4 GTS che sfrutta l’iniezione di acqua in aspirazione per abbattere le temperature, migliorare la densità della carica e, quindi, aumentare il rapporto geometrico di compressione o la pressione di sovralimentazione.
Si tratta di una tecnologia che venne adottata già ai tempi della Seconda Guerra Mondiale sui motori destinati all’aeronautica e che ora alcuni costruttori stanno rispolverando per i loro modelli più prestazionali.
Tags: turbocompressore