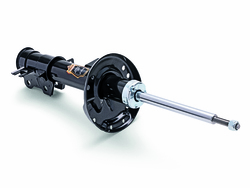
Con una gamma completa e una logistica di eccellenza che permette di soddisfare tutte le esigenze del mercato aftermarket, Japanparts torna a parlare di ammortizzatori per spiegare quali sono i dettagli e i processi di lavorazione che rendono un ammortizzatore sicuro, affidabile e performante nel tempo.
Quando si parla di ammortizzatori, si parla di un componente fondamentale per la sicurezza su strada: per questo è importante non soltanto verificare il loro stato di usura, ma anche e soprattutto affidarsi a prodotti di qualità certa.
Ma se a prima vista gli ammortizzatori possono sembrare tutti uguali, come si può capire quando un prodotto rispecchia davvero gli elevati standard del primo impianto? Per dare una risposta a questo quesito è necessario conoscere l’azienda produttrice ed entrare nel dettaglio tecnico di materiale e test a cui vengono sottoposti i prodotti.
Japanparts, azienda che vanta un catalogo sospensioni particolarmente ricco (con più di 13.600 articoli in gamma e un magazzino dedicato di 31.100 mq) che le permette di soddisfare le esigenze non solo del circolante asiatico ma anche di quello europeo, ci aiuta a rispondere a queste domande e a sciogliere i dubbi su come si realizza un ammortizzatore performante, affidabile e di lunga durata.
Affidabilità e durata: attenzione ai dettagli
Un ammortizzatore sicuro è un ammortizzatore che dura nel tempo, mantenendo uno standard elevato di prestazioni. “Per poter assicurare l’affidabilità del prodotto anche dopo migliaia di chilometri di percorrenza, gli ammortizzatori devono essere sottoposti a particolari lavorazioni, e numerosi test e prove di collaudo che fanno la differenza fra un prodotto di elevata qualità e uno di scarso valore” spiega l’azienda di Verona.Nel raccontare come vengono realizzati gli ammortizzatori che Japanparts propone al mercato dell’aftermarket indipendente, l’azienda cita come diversi studi sperimentali abbiano dimostrato che effettuare la finitura della superfice prima della placcatura può migliorare significativamente la resistenza alla corrosione dello stelo.
“Noi utilizziamo un acciaio al cromo di alta precisione, che è stato sottoposto a 20 processi di trattamento di precisione, mentre mediamente gli altri produttori ne effettuano 12” spiega Japanparts. “Inoltre, tutti i pistoni sono placcati e lucidati con apparecchiature ad alta precisione importate dal Giappone” sottolinea l’azienda.
“Un’altra lavorazione a cui sottoponiamo i nostri prodotti (a differenza di altri produttori) – sottolinea Japanparts – prevede un passaggio con la lucidatrice longitudinale e il macchinario per la deidrogenazione, utili per migliorare la tenuta e la resistenza alla corrosione e quindi per garantire una lunga durata di servizio”.
Inoltre, il prodotto è sottoposto a un trattamento all’acqua galvanica, utilizzato per assicurare la perfetta lubrificazione del pistone degli ammortizzatori e identificare eventuali micro fessure.
L’azienda evidenzia anche l’impiego di un robot articolato per la saldatura degli ammortizzatori “riconosciuto come il migliore al mondo” sottolinea Japanparts. E precisa: “i parametri sono continuamente monitorati e la saldatura è completamente automatica, il che riduce notevolmente le scorie di saldatura. La qualità della saldatura è perciò conforme allo standard nazionale e soddisfa al 100% le esigenze dei clienti” conclude l’azienda.
“A un attento controllo visivo – dichiara Japanparts - si può facilmente notare che il piattello del nostro ammortizzatore è piatto e presenta una saldatura rinforzata; i giunti di saldatura sono lisci, stretti e resistenti e hanno una lunga durata, mentre le saldature di prodotto di scarsa qualità presentano evidenti scorie”.
Infine, ammortizzatori e molle elicoidali sono verniciati con vernice elettroforetica (“la più grande apparecchiatura elettroforetica nel mercato post-vendita” sottolinea l’azienda); una soluzione che assicura una forte resistenza all'ossidazione e alla corrosione, quindi una risposta maggiore dell’ammortizzatore, oltre che una sua maggior durata.
Test di collaudo per la massima sicurezza
Gli ammortizzatori vengono sottoposti a numerosi test che verificano le performance del prodotto in termini di sicurezza, affidabilità e durata nel tempo.Ovviamente ci sono delle variabili che determinano la durata di un ammortizzatore, a seconda dello stile di guida e del tipo di fondo stradale; proprio per questo i prodotti vengono sottoposti a test estremi, che possano permettere di garantire l’affidabilità e il comfort di guida in qualsiasi situazione.
“Secondo i dati basati sui test dinamometrici, - riporta Japanparts – su strade convenzionali un ammortizzatore viene sollecitato circa 1.500 volte ogni chilometro; gli ammortizzatori Japanparts vengono sottoposti a 10 milioni di attivazioni, pari a circa 6.666 km, contro i 3 milioni di attivazioni mediamente utilizzati per i test da altri produttori secondo gli standard generali di mercato.”
“In pratica – sottolinea l’azienda di Verona - l’ammortizzatore Japanparts sottoposto a test lavora circa 7 milioni di volte in più rispetto agli altri: un dato molto significativo che dimostra l’ottima qualità e la straordinaria performance dell’ammortizzatore che proponiamo al mercato”.
Un altro numero significativo che distingue gli ammortizzatori Japanparts sul mercato è il risultato del test di forza, che “per i nostri ammortizzatori è pari a 6.656 kg, mentre il massimo risultato ottenuto per prodotti della stessa categoria è di 6.356 kg” dichiara l’azienda.
Un altro importante banco di prova per gli ammortizzatori è il test di tenuta. La prova consiste nel caricare l’asta dell’ammortizzatore con diametro maggiore o uguale a 15 mm con un carico di tensione parti a 22 kn alla velocità di 50 mm/min; in queste condizioni l’asta del pistone deve rimanere integra. “Un test che gli ammortizzatori Japanparts superano brillantemente” dichiara l’azienda.
Infine, tra le prove cui vengono sottoposti gli ammortizzatori della società veronese, segnaliamo il test in nebbia salina, che permette di verificare la resistenza alla corrosione dello stelo.
Il film di verniciatura sulla superfice non si deve modificare dopo il test in nebbia salina di 150 h. In seguito viene effettuato un processo di elettroforesi per 500 h; la verniciatura non subisce cambiamenti. Infine, dopo 48 h di test in nebbia salina (72 h in caso di diametro spesso) la cromatura dello stelo sarà libera da corrosioni e scorie di rivestimento.
L’offerta sospensioni e ammortizzatori di Japanparts Con più di 13.600 articoli in gamma e un magazzino dedicato di 31.100 mq, Japanparts Srl offre una delle gamme più complete in Europa. L’intera offerta comprende ammortizzatori anteriori e posteriori, compresi silent block e relativi supporti. Gli ammortizzatori sono la famiglia di prodotti più venduti della gamma Japanparts, con una qualità di prim'ordine, un prezzo competitivo e circa 2.200 referenze disponibili che coprono l'intero parco circolante. |
Tags: ammortizzatori japanparts