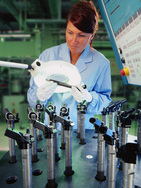
Consumi di carburante più vantaggiosi, potenze più elevate, maggiore rapidità di risposta alle variazioni di carico, maggiore facilità di avviamento a freddo e un superiore contenimento delle emissioni inquinanti: questi i risultati raggiunti dai sistemi di iniezione di ultima generazione.
Anche se i sistemi a iniezione hanno fatto parlare molto di sé soprattutto negli ultimi 25 anni, grazie all’incredibile evoluzione tecnologica da essi subita, in realtà la loro nascita risale addirittura agli anni ’30. In particolare l’iniezione, congenita nei motori a gasolio, riduce notevolmente i consumi anche in quelli a benzina. L’obiettivo dell’iniezione è quello di superare le perdite di carico nel sistema di aspirazione, la difficoltà di regolazione della dosatura, resa difficile dalla dipendenza da un alto numero di parametri operativi del motore e il condizionamento nel dimensionamento dei condotti di aspirazione. I sistemi di iniezione offrono quindi consumi di carburante più vantaggiosi, potenze più elevate, maggiore rapidità di risposta alle variazioni di carico, maggiore facilità di avviamento a freddo e un superiore contenimento delle emissioni inquinanti. L’ultima frontiera dei sistemi d’iniezione di benzina è quella diretta, con il combustibile iniettato direttamente nella camera di scoppio che consente un’esplosione della miscela più immediata e quindi rendimenti ottimizzati. Ma se per il benzina l’elevata resa dell’iniezione diretta si avverte soprattutto ai bassi regimi, per quanto riguarda i propulsori a gasolio, che utilizzano la compressione per la combustione invece della scintilla della candela, i rendimenti sono nettamente superiori durante tutto l’arco di giri. Ormai la maggior parte dei propulsori Diesel sono a iniezione diretta di gasolio ad altissima pressione (i Common Rail di seconda e terza generazione raggiungono i 1.600 bar), per una migliore polverizzazione, che consente minori consumi. Principalmente sono due i sistemi di iniezione diretta di gasolio più utilizzati: il Common Rail e l’iniettore-pompa. Il primo, conosciuto anche come sistema ad accumulatore (Common Rail) con iniettori ad apertura comandata, è stato sviluppato per essere flessibile e permettere un perfetto controllo dei tempi d’iniezione, per operare con alti valori di pressione, per controllare l’usura, garantendo le tenute per tutta la vita del sistema e per operare con iniettori pilota o a due molle. Queste condizioni sono imposte dal suo utilizzo su motori con alti valori del rapporto di compressione sovralimentati. La flessibilità sul tempo d’iniezione permette di lavorare nelle condizioni ottimali per ciascun punto di funzionamento. I suoi componenti principali sono la pompa ad alta pressione, il regolatore di pressione, l’accumulatore ad alta pressione (Common Rail), i condotti ad alta pressione, l’unità di controllo elettronico e gli iniettori. Oltre alla logica importanza che assume la pompa, il regolatore di pressione e l’accumulatore, grandi sviluppi si stanno ottenendo sul fronte degli iniettori, gestiti sempre più, come vedremo, da un’elettronica raffinata. Vediamo come funzionano. Il combustibile passa attraverso l’orifizio ed entra nel volume di controllo; la pressione agisce sulla parte superiore dell’asta di spinta. Quando il solenoide viene alimentato si apre l’orifizio, la pressione nel volume di controllo si riduce e l’iniettore si apre. Interrompendo la corrente che alimenta il solenoide, l’iniettore si chiude. Quando la pressione nel volume di controllo aumenta, l’asta di spinta chiude l’iniettore. La durata dell’iniezione, la pressione del combustibile nel collettore e il flusso attraverso l’iniettore determinano la quantità di combustibile iniettato. L’iniettore viene aperto e chiuso dalla centralina nei tempi definiti dalla mappatura del motore.Il sistema iniettore-pompa è costituito da un circuito a bassa pressione, dotato di pompa di alimentazione e filtro, che alimenta tanti iniettori-pompa quanti sono i cilindri del motore. Un unico albero a camme aziona i pistoncini di ciascun elemento pompante. Con questo sistema si elimina la tubazione ad alta pressione.
Le novità proposte dai produttori
Il nuovo Common Rail di Delphi con tecnologia MultecTM usa un unico iniettore solenoide progettato per ottimizzare il tasso di carburante, la forma dello spruzzo e l’accuratezza. Con questo sistema vengono fornite quantità d'iniezione più piccole e si ottiene maggior precisione nell’emissione. Queste caratteristiche, unite a strategie del “cappio chiuso”, rendono possibili ottimi livelli di emissioni e performance acustiche.
In aggiunta allo sviluppo dell’iniettore di prossima generazione Multec, Delphi sta sviluppando un iniettore unico, basato sul piezo per meglio soddisfare le richieste poste dalle nuove regolamentazioni sulle emissioni Euro V e dalle severe norme U.S.
Le aspettative sono che la nuova tecnologia riduca del 25-30% (in confronto all’attuale tecnologia piezo Common Rail) le emissioni nella sua prima fase di implementazione. La nuova tecnologia piezo valve sviluppata da Delphi permetterà al sistema di iniezione Delphi Piezotec di iniettare da sette a più getti di iniezione per ciclo con estrema accuratezza nella quantità di carburante pilota iniettato, prima e dopo l’emissione. Il design consente una riduzione apprezzabile degli intervalli tra gli eventi, dando ai progettisti piena libertà di determinare il flusso di carburante attraverso il tempo della combustione.
Sul fronte dell’autoriparazione, Delphi ha presentato un nuovo strumento progettato per testare e diagnosticare guasti specifici sui sistemi Common Rail. In grado di fornire una lettura diretta dell’alta pressione e di misurare il flusso di bassa pressione, il dispositivo di misurazione della pressione e della dispersione “sealed rail” YDT278 permette ai tecnici di identificare velocemente i problemi di alimentazione su qualsiasi sistema Common Rail.
Il sistema Delphi Multec Common Rail è montato su Renault/Nissan, PSA Peugeot Citroën, Hyundai/Kia, SsangYong, e Ford/Premier Auto Group. L’impianto migliorato entrerà in produzione su Renault e Hyundai dal primo 2004. A partire dal 2005 altri quattro costruttori impiegheranno il sistema Delphi per i propri modelli.
La terza generazione Common Rail proposta da Bosch prevede un funzionamento con iniettori Piezo-Inline compatti, a inserimento rapido. Bosch ha finora improntato le generazioni del Common Rail sulla pressione d’iniezione: la prima generazione era caratterizzata da una pressione di 1.350 bar, la seconda generazione da una pressione di 1.600 bar. Con il passaggio alla terza generazione, l’attenzione è focalizzata sui dettagli tecnici del sistema, che per ora funziona con una pressione invariata di 1.600 bar. Una particolarità della terza generazione del Common Rail è rappresentata dagli iniettori Inline, il cui elemento piezo è integrato nel vano iniettore, in posizione molto vicina alla punta dell’iniettore. I nuovi iniettori sono realizzati con il 75% in meno di componenti in movimento e di massa, con il vantaggio di poter intervenire a una velocità doppia rispetto agli iniettori piezo e alle valvole magnetiche utilizzati fino ad oggi. Bosch sta lavorando per aumentare la pressione a oltre 2.000 bar agli iniettori, attraverso il trasferimento della pressione, senza dover aumentare la pressione del sistema generale ed è allo studio anche la realizzazione di iniettori con geometria d’iniezione variabile.
Un altro caso è quello della Firad, presente da oltre trent’anni nel campo dell’iniezione Diesel con la produzione di polverizzatori per tutte le applicazioni “automotive”. L’azienda riscontra un crescente consenso e apprezzamento non solo in Italia, ma anche a livello europeo e mondiale. Il costante impegno e i continui investimenti hanno permesso all’azienda di avere non solo una gamma idonea a soddisfare le crescenti esigenze dei clienti ma anche e soprattutto di raggiungere un livello qualitativo sempre più elevato e orientato verso i prodotti più evoluti del mercato del Diesel. I prodotti di punta dell’azienda sono i polverizzatori (sia per Aftermarket che per primo impianto) per i nuovi sistemi di tipo Common Rail, iniettori pompa e doppio stadio con una gamma sempre più vasta e di estrema affidabilità.