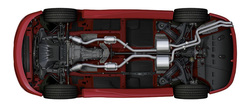
I sistemi di scarico moderni hanno raggiunto livelli tecnologici molto elevati, un’evoluzione obbligata e in larga misura imposta dalle moderne normative antinquinamento. I sistemi di scarico moderni hanno raggiunto livelli tecnologici molto elevati, un’evoluzione obbligata e in larga misura imposta dalle moderne normative antinquinamento. Ma i condotti di scarico sono anche determinanti per il raggiungimento di prestazioni superiori. I sistemi di scarico moderni hanno raggiunto livelli tecnologici molto elevati, un’evoluzione obbligata e in larga misura imposta dalle moderne normative antinquinamento. Ma i condotti di scarico sono anche determinanti per il raggiungimento di prestazioni superiori. Vediamo alcuni trucchi e segreti che si celano dietro a quelli che sembrano semplici tubi. I sistemi di scarico moderni hanno raggiunto livelli tecnologici molto elevati, un’evoluzione obbligata e in larga misura imposta dalle moderne normative antinquinamento. Ma i condotti di scarico sono anche determinanti per il raggiungimento di prestazioni superiori. Vediamo alcuni trucchi e segreti che si celano dietro a quelli che sembrano semplici tubi. I sistemi di scarico moderni hanno raggiunto livelli tecnologici molto elevati, un’evoluzione obbligata e in larga misura imposta dalle moderne normative antinquinamento. Ma i condotti di scarico sono anche determinanti per il raggiungimento di prestazioni superiori. Vediamo alcuni trucchi e segreti che si celano dietro a quelli che sembrano semplici tubi.
Il 50% dell’energia prodotta dal motore se ne va attraverso i condotti di scarico. E allora? Molto semplice, dobbiamo pensare di utilizzarla al meglio. Dato che nella maggioranza dei casi non possiamo recuperarla, quest’energia va sfruttata nel migliore dei modi, ad esempio ponendo il catalizzatore in prossimità dei collettori di scarico per velocizzare il raggiungimento delle temperature di esercizio necessarie ai processi di conversione operati dal catalizzatore stesso. Ma procediamo con ordine, per cercare di capire quali sono gli aspetti tecnici più importanti legati ai condotti di scarico e alla loro produzione. A fine articolo vi presenteremo un paio di applicazioni di primo impianto per vedere come i diversi produttori hanno affrontato l’argomento.La velocità dei gas
Una prima importante distinzione riguarda la velocità di flusso dei gas di scarico rispetto a quelli di aspirazione. Se nel secondo caso si può parlare di velocità medie, nel migliore dei casi, prossime ai 45m/s, nel caso dei gas combusti in uscita dal motore le cose sono molto diverse e, a pieno carico, un motore a combustione interna può anche “sparare” fuori i gas esausti a una velocità prossima, o anche superiore, ai 70m/s. Per coloro che sono meno tecnici basti sapere che le perdite di carico crescono notevolmente con la velocità e quindi un disegno accorto dei collettori e dei condotti di scarico è fondamentale per assicurare un flusso corretto.
Quest’ultimo fatto è di importanza fondamentale, perché se lo smaltimento dei gas non avviene correttamente, gli organi dotati di moto alternato, i pistoni nella fattispecie, incontreranno quella che viene definita in gergo contropressione allo scarico, ossia una sorta di impedimento allo smaltimento della miscela combusta con ovvie perdite di potenza e coppia.
Il turbo compressore“a tutto gas”
Proprio l’elevata temperatura e la velocità con cui i gas fuoriescono dalla testa hanno portato all’ideazione del concetto di turbocompressore azionato dai gas di scarico: un modo intelligente per recuperare l’energia che altrimenti andrebbe persa nell’atmosfera. Certo non tutta l’energia potrà essere così recuperata, ma una buona parte di essa. In pratica, applicando all’uscita dei condotti di scarico una turbina centripeta, è possibile ottenere del lavoro da trasferire a un compressore, direttamente collegato alla turbina, che potrà elevare il rendimento volumetrico del motore, immettendo una maggiore quantità di aria fresca nello stesso. Il tutto sfruttando una pressione superiore a quella atmosferica.
Anche in questo caso il design dei collettori di scarico, così come quello della chiocciola della turbina, sarà fondamentale per ottenere il flusso corretto. Collettori e turbina piccoli daranno una risposta più immediata all’acceleratore, ma costituiranno un problema agli alti regimi, dove la contropressione si farebbe sentire in modo pesante. Se i collettori e la turbina sono invece di dimensioni esagerate, il flusso sarebbe caratterizzato da una velocità troppo bassa e la portata dei gas non sarebbe sufficiente a mettere in rotazione il turbocompressore, con conseguenti ritardi di risposta e guidabilità della vettura ridotta ai minimi termini. In corrispondenza dei regimi più alti si assisterebbe a impennate di potenza e coppia molto più difficili da gestire e, più in generale, di scarsa fruibilità, almeno per chi l’auto la utilizza per scopi turistici.
Materiali e durata
Un altro problema legato strettamente ai condotti di scarico è quello dei materiali. Il sistema di scarico è infatti sottoposto a shock termici molto elevati e pertanto dilatazioni e cedimenti di resistenza strutturale sono sempre in agguato. Proprio per questo motivo i materiali normalmente scelti sono quelli in grado di far fronte alle sollecitazioni sopra menzionate e in generale si tratta di acciai zincati o inossidabili. Anche in questo caso un’ulteriore precisazione è d’obbligo, perché è bene ricordare anche l’aggressività chimica generata dai gas. Aggressività ulteriormente enfatizzata dalla presenza di calore elevato. Non a caso anche nei sistemi più economici è comunque prevista la zincatura.
Il processo di corrosione cui gli scarichi sono soggetti è anche strettamente legato all’uso che si fa della vettura. In altre parole, quando un motore raggiunge le corrette temperature di esercizio, il flusso dei gas caldi, in arrivo dal motore, “asciuga” per così dire le pareti dei condotti stessi, asportando quella condensa che se lasciata sul posto innescherebbe i tradizionali processi corrosivi. Se però il mezzo viene utilizzato quotidianamente per pochi chilometri, troppo pochi perché il motore raggiunga e mantenga per un certo tempo le corrette condizioni termiche di esercizio, allora i processi di corrosione avranno la meglio e la durata del condotto di scarico verrà seriamente compromessa.
La sonda Lambda:“il controllore” degli scarichi
Abbiamo poi parlato, nella fase introduttiva dell’articolo, del problema delle emissioni inquinanti. Questa spada di Damocle sospesa sulla testa di ogni costruttore ha obbligato i tecnici delle varie case a mettere in campo soluzioni costose per la riduzione e l’eliminazione delle emissioni dichiarate nocive per l’uomo e per l’ambiente. Sono così nati e si sono sviluppati i catalizzatori, sia per i motori Diesel sia per i propulsori a benzina. Si tratta di elementi costosi, che per funzionare richiedono particolari condizioni di esercizio, soprattutto in termini di temperatura e composizione della miscela allo scarico. Proprio per questo motivo è stato quasi obbligatorio montare le cosiddette sonde Lambda, in grado di monitorare il processo di combustione e, successivamente, il lavoro del convertitore.
Già, perché prima dell’avvento delle motorizzazioni Euro 4, era sufficiente verificare se la miscela dei gas combusti in uscita dal motore fosse stechiometricamente corretta. Se l’evento non si verificava (e il controllo era appunto affidato alla sonda Lambda posta prima del catalizzatore), il controllo elettronico del motore prevedeva di modificare il rapporto A/F (air/fuel) per ottenere i risultati corretti. Nulla però si poteva sapere sul corretto lavoro del catalizzatore, che una volta usurato poteva portare a processi di conversione non completi. Per questo motivo, con le più stringenti normative Euro 4, le cose sono cambiate ulteriormente e i costruttori sono stati obbligati a monitorare anche il lavoro del catalizzatore ponendo quindi una sonda Lambda a valle dello stesso.
Silenziatori: il giusto rombo del motore
Infine, ma sicuramente non in ordine di importanza, gli ingegneri dedicati allo studio dei condotti di scarico hanno dovuto sempre pensare a come neutralizzare la rumorosità generata dal processo di combustione. Questo è stato ottenuto con l’uso di opportuni silenziatori, realizzati chiaramente in modo differente a seconda del tipo di vettura e, in ogni caso, in ottemperanza ai massimi livelli di rumorosità imposti dal legislatore. Le vetture sportive vengono normalmente dotate di silenziatori più permeabili, mentre quelle per uso strettamente turistico, o di gamma più elevata, sono solitamente dotate di sistemi particolarmente silenziosi.
Conclusioni
Ricapitolando brevemente possiamo dire che ai moderni sistemi di scarico oggi vengono richieste prestazioni che per essere raggiunte necessitano tecniche produttive e materiali di ultimissima generazione. Gli obiettivi comuni a tutti gli scarichi, ma chiaramente con peso differente a seconda dell’impiego della vettura, sono i seguenti: leggerezza, resistenza alla corrosione, capacità di raggiungere le temperature di esercizio nel minor tempo possibile, garantire un flusso esente da perdite di carico eccessive e assicurare la sonorità cercata, nel caso sia di scarico silenzioso sia di tipo sportivo.
Vediamo di seguito alcune moderne soluzioni messe a punto da un noto costruttore di sistemi di scarico.
Soluzioni OE: la Bmw M3
Tra gli esempi applicativi presenti sul mercato ci è sembrato interessante prendere in considerazione una vettura particolarmente sportiva. In questi casi, infatti, la realizzazione dello scarico rappresenta per il costruttore e per il fornitore una sfida estremamente importante.
La M3 costruita da BMW è un lampante caso di vettura stradale a elevatissime prestazioni. Per la realizzazione dello scarico i tecnici bavaresi hanno affiancato quelli di ArvinMeritor, noto produttore, tra le altre cose, di scarichi per primo equipaggiamento.
Gli obiettivi posti per il progetto M3, furono ambiziosi sin dall’inizio. Si tenga conto inoltre che a breve verrà presentata la nuova M3 che a quanto sembra monterà un V8 e quindi un sistema di scarico totalmente differente da quello che oggi equipaggia il 6 cilindri da 3.254cc dell’attuale M3.
Spiegare nel dettaglio e raccontare le fasi dello sviluppo di questo scarico sarebbe troppo lungo e complesso. Basti però sapere che gli obiettivi posti dal progetto hanno implicato il superamento di alcune oggettive difficoltà. Lo scarico, infatti, doveva essere compatibile con la serie delle vetture M qui di seguito elencate: M3, per l’appunto, M Roadster ed M Coupè.
Altri target fissati a priori riguardavano la limitazione del peso, pari a massimo 50kg, la capacità di ottemperare alle più severe norme antinquinamento e di rumorosità (comprese quelle americane), l’affidabilità sulla lunga durata, le prestazioni (basse contropressioni) e naturalmente la resistenza strutturale. Tali obiettivi sono stati raggiunti grazie all’impiego di tecnologie di produzione ultramoderne e all’uso di materiali speciali.
Per quanto riguarda le tecnologie produttive, l’aspetto più interessante è legato al processo di modellazione ad alta pressione, noto anche con IHU (internal high-pressure molding). Per quanto riguarda invece i materiali, la maggior parte dei condotti di scarico è stata realizzata con acciai inossidabili austenitici, particolarmente resistenti alla corrosione e alla temperatura. Nota da non trascurare la realizzazione dei collettori di scarico con spessore della parete pari a solo 1mm.
Un ulteriore discorso lo merita il catalizzatore metallico, anch’esso particolarmente sofisticato e che, tra le sue caratteristiche principali, vanta una densità delle celle pari a 200 per pollice quadrato (corrispondenti ad un valore di circa 31 celle per cm2).
La particolare conformazione del pianale e del sistema di trasmissione dell’M3 ha inoltre richiesto una geometria di assemblaggio dell’intero sistema di scarico tale per cui il silenziatore, con lo scopo di contenere la rumorosità al di sotto dei 75dB, è stato posizionato nella zona posteriore. Notevole la sua capacità con un volume di 40dm3.
Un ultimo appunto riguarda la conformazione particolarmente sportiva dei collettori di scarico e dei condotti. Come si conviene a un’auto con velleità sportive, lo scarico svolge un compito determinante. Proprio per questo motivo la conformazione dei collettori è stata pensata per avere lunghezza identica per ogni cilindro e un accoppiamento funzionale in linea con l’ordine di accensione del motore dell’M3, che risulta pari a: 1-5-3-6-2-4.
Sul fronte dei condotti segnaliamo solamente un dato veramente eccezionale: la perdita di carico massima lungo il percorso di scarico, in corrispondenza di un regime pari a 8.000 giri/min, risulta di soli 300mbar.
Soluzioni OE: la Chevrolet Corvette Z06
Come per il primo esempio considerato, anche il sistema di scarico della Corvette Z06 del 2001 è stato realizzato in collaborazione con ArvinMeritor. La particolarità di questo impianto sta nell’aver utilizzato il titanio per realizzare il silenziatore. Una soluzione che ha consentito di abbattere sensibilmente il peso (l’intero sistema pesa solo 26 pound, circa 12kg) e di sostituire un intero assieme che nella sua versione precedente pesava ben 44 pound (circa 20kg).
Questa tecnologia che fa uso del titanio è stata definita da ArvinMeritor “T3”, a significare Titanium, Technology and Testing, e ha permesso di raggiungere traguardi strutturali e di affidabilità una volta impensabili per un’auto di serie, seppure di stampo sportivo. Per la realizzazione di questo scarico sono stati appositamente adattati i processi di saldatura, formatura a freddo e stampaggio.