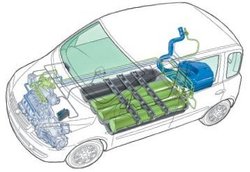
Questo tipo di alimentazione è sempre più diffusa e ora, con il petrolio ben oltre i 100 dollari al barile, sono sempre di più gli utenti che prendono in considerazione la possibilità di installare sulle proprie vetture un sistema di alimentazione a gas.
In realtà sono sempre di più anche i costruttori che offrono impianti a gas in primo equipaggiamento. Il layout di un tipico sistema di alimentazione a gas si è ormai consolidato in questi ultimi anni e, malgrado siano numerose le aziende in grado di produrre tali impianti, i componenti di base, e il principio di funzionamento, sono sostanzialmente simili.L'idea che sta alla base dei moderni sistemi di alimentazione a gas è quella di montare il controllo elettronico dell'impianto direttamente in serie a quello del sistema a benzina. In pratica il cervello di controllo di un impianto a gas analizza i segnali in uscita dalla centralina del sistema a benzina e li tramuta in segnali adatti per pilotare gli iniettori del gas. Per questo motivo, e non solo, tali impianti vengono molto spesso definiti sequenziali-fasati. Il concetto di sequenziale, così come quello di fasato, assume chiara espressione se si pensa a quanto detto poco sopra.
Scendendo più in dettaglio, un impianto a gas si compone di alcuni elementi tipici tra cui il riduttore/vaporizzatore, il rail degli iniettori, gli iniettori stessi, il filtro, la centralina e naturalmente il serbatoio e la presa di carica (bocchettone di rifornimento). Come anticipato poco sopra, il controllo elettronico motore, cioè la centralina, si occupa di trasformare i tempi di iniezione degli iniettori a benzina in tempi di iniezione opportuni del sistema a gas. In realtà perché ciò avvenga correttamente servono anche gli elementi di cui abbiamo parlato. Il riduttore/vaporizzatore, in particolare, deve consentire, come dice il nome stesso, il passaggio del gas dallo stato liquido a quello gassoso (in realtà ciò è valido per il GPL, mentre per il metano le cose vanno in modo leggermente differente, si veda più avanti). Per raggiungere questo obiettivo il sistema fa uso anche del liquido refrigerante del motore che, scorrendo in un opportuno circuito ricavato all'interno del vaporizzatore stesso, aiuta il processo di vaporizzazione.
Il filtro a sua volta deve essere in grado di bloccare tutte le particelle dannose contenute all'interno del gas mentre, affinché siano verificati i parametri specifici più importanti di funzionamento del motore, opportuni sensori sono montati all'interno del circuito stesso. Una delle soluzioni tipiche è quella che vede il sensore di pressione e temperatura alloggiati nel rail degli iniettori mentre il sensore che monitora la temperatura del liquido refrigerante è integrato direttamente nel riduttore/vaporizzatore.
Il funzionamento sequenziale fasato è la vera "trovata di genio" dei moderni impianti a gas. Grazie a essa, infatti, vengono preservate tutte le strategie previste in sede di progetto dal costruttore. Tra queste, sicuramente, vanno ricordate il taglio dell'alimentazione, il funzionamento del canister, il controllo del minimo, anche in presenza di accensioni e spegnimenti di carichi aggiunti (come ad esempio il climatizzatore o il servosterzo), e naturalmente i sistemi di sicurezza come il controllo di stabilità e di trazione. A proposito di questi ultimi basti pensare che quando un sistema di controllo della trazione e della stabilità interviene, le azioni intraprese prevedono, tra le altre, l'intervento sulla posizione del corpo farfallato e sulla portata di combustibile da inviare agli iniettori e, quindi, sull'erogazione di coppia da parte del motore. A tutto questo aggiungiamo altri parametri come ad esempio il limitatore di giri e la gestione del ricircolo dei gas di scarico.
Vale la pena segnalare che una delle differenze macroscopiche tra metano e GPL è legata allo stato fisico dei due gas all'interno del circuito. Mentre il metano rimane sempre allo stato gassoso, il GPL è allo stato liquido fino al riduttore/vaporizzatore per poi passare allo stato gassoso attraverso il processo di vaporizzazione. Un'ulteriore grande differenza è dovuta alla pressione con cui i gas vengono stoccati nel serbatoio. L'ordine di grandezza dei valori di pressione è notevole e pari all'incirca a 10.
In altre parole se il GPL viene caricato nei serbatoi a 20 bar, il metano deve esserlo a 200 bar. Questo spiega anche perché determinati componenti come le bombole hanno una struttura sensibilmente differente.
Come anticipato nel paragrafo precedente, il metano, a differenza del GPL, rimane sempre allo stato gassoso. Nel caso del gas naturale, quindi, il vaporizzatore svolge la funzione di riduttore di pressione. Il gas in arrivo dal serbatoio viene quindi portato alla pressione di esercizio con cui verrà immesso nel rail iniettori e quindi, attraverso gli iniettori stessi, nel collettore di aspirazione (iniezione indiretta).
Il gas è amico dell'ambiente
I motori endotermici funzionanti a gas offrono vantaggi indiscutibili sia in termini di emissioni che di consumi. Per quanto riguarda le prime, in particolare, a migliorare sono le emissioni di polveri sottili, pressoché nulle con l'alimentazione a gas, e la minor quantità di anidride carbonica. Questo è anche il motivo per cui quando vi sono blocchi del traffico ai veicoli alimentati a gas (metano o GPL che sia) è permesso comunque circolare. Se volessimo elencare la lista dei vantaggi ottenibili con l'alimentazione a gas possiamo senz'altro dire che: la combustione non produce particolato, viene ridotta sensibilmente la produzione di CO (monossido di carbonio), il maggior potere antidetonante consente di aumentare il rapporto geometrico di compressione e la sua disponibilità nel futuro sembra essere elevata. Per contro, con il gas l'autonomia rispetto alla benzina è minore, e viene richiesto un maggior spazio per i serbatoi. La rete di distribuzione, infine, soprattutto per il metano, non è ancora pienamente sviluppata.
I motori a combustione interna e il gas
L'uso di gas come combustibile per i motori a ciclo Otto non rappresenta un problema se si presta attenzione a un fatto importante. Il gas, infatti, rispetto alla benzina, offre minore potere lubrificante e, in generale, porta a condizioni di "secchezza" che a lungo andare possono portare al danneggiamento delle sedi valvola. Il problema è evitabile in due differenti modi: il primo è quello di avere l'accortezza di far funzionare il motore periodicamente con benzina. In questo modo il maggior potere lubrificante della benzina aiuta la conservazione dei componenti. Sempre parlando di motori non studiati appositamente per funzionare a gas, la seconda accortezza è quella di accendere il propulsore con l'alimentazione a benzina e passare successivamente a gas. I primi istanti di funzionamento di un motore a combustione interna, infatti, sono i peggiori, almeno dal punto di vista della lubrificazione. L'accensione a benzina evita usure eccessive proprio durante questo periodo. In realtà questo genere di problemi sono stati ora sorpassati grazie alle nuove tecnologie con cui vengono realizzate le testate dei motori che molte volte, già in fabbrica, nascono idonee per funzionare con il gas. Quest'ultimo però, non bisogna dimenticarlo e per questo lo ripetiamo, ha un netto vantaggio rispetto alla benzina: il numero di ottano superiore che in termini pratici significa minor attitudine alla detonazione. Il suo minor potere energetico rispetto alla benzina richiede di intervenire su alcuni parametri del motore per migliorarne le prestazioni. Anticipare l'accensione è una delle strategie che si possono utilizzare senza per questo andare incontro alla detonazione.
Un'ulteriore attenzione andava dedicata, tempo fa, al problema del corretto rapporto aria/benzina che, una volta alterato, poteva portare al danneggiamento dei catalizzatori o perlomeno a una loro precoce usura. Oggi con i sistemi sequenziali fasati tutto questo è pressoché un ricordo e la presenza delle sonda lambda con controllo in retroazione consente di gestire sempre al meglio il problema.