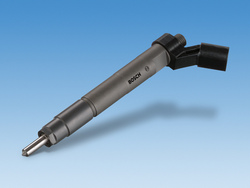
Un tempo si diceva: è come un motore Diesel: parte piano, ma una volta scaldato non lo ferma nessuno. Oggi questa storica affermazione ha perso validità: le nuove motorizzazioni sono efficienti da subito, ma a fermare il Diesel è spesso l’elettronica.
In Italia un auto su cinque ha un motore Diesel. Non solo, il trend è in crescita e a meno di una improbabile inversione di tendenza, le auto alimentate a gasolio supereranno nei prossimi anni quota 50% dell’intero parco circolante. Uno dei motivi di una crescita così imperiosa è il particolare regime fiscale presente in Italia, che ha fatto sparire una pesante tassa come il super bollo e che, grazie a un diverso peso delle imposte sui carburanti, garantisce un prezzo del gasolio più basso di quello della benzina (mentre, ad esempio, la produzione ha costi invertiti). Il successo del Diesel non è però circoscritto ai soli confini nazionali; in tutta Europa questo tipo di motori si sta diffondendo con successo, al punto che oggi anche molte auto considerate sportive sono alimentate a gasolio.Le nuove tecnologie sono le vere artefici di un simile successo, consentendo prestazioni comparabili a quelle dei motori a benzina e, in determinate condizioni di impiego, addirittura superiori. I sistemi di iniezione Common Rail e iniettori pompa hanno migliorato il rendimento dei motori; le nuove candelette sono sempre più performanti e hanno azzerato i tempi di preriscaldamento della camera di combustione; la rumorosità è molto contenuta, grazie all’utilizzo degli iniettori piezoelettrici; i turbocompressori, primi artefici dell’aumento delle prestazioni, stanno di nuovo tornando in auge, grazie alla sperimentata tecnologia a geometria variabile e alle nuove applicazioni multistadio.
Vediamo in dettaglio come questi sistemi agiscono e che impatto abbiano avuto sul mondo che ruota attorno ai motori Diesel.
I nuovi Diesel
L’iniezione, come detto, è uno dei settori in cui i grandi marchi stanno investendo per migliorare l’efficienza dei motori Diesel. Avere grandi pressioni disponibili al momento dell’iniezione è fondamentale per riuscire a nebulizzare il carburante in finissime particelle. Il risultato è una miscela aria e gasolio ben amalgamata, cosicché la combustione è il più possibile completa e senza residui. Se il gasolio iniettato brucia completamente, non vi sono sprechi e il motore è più performante. L’uso di iniettori elettronici, inoltre, ha risolto altri due grandi problemi propri dei motori Diesel: rumorosità e inquinamento. Il classico “borbottio” proprio dei trattori è da sempre una caratteristica di questo tipo di propulsori: tale rumorosità è dovuta all’improvvisa detonazione della carica all’interno del cilindro.
Al contrario dei motori a benzina, in cui l’accensione avviene grazie a una scintilla concentrata in un punto specifico, per poi espandersi attraverso un “fronte di fiamma” all’interno della camera di combustione, in un motore Diesel è la pressione e il conseguente aumento di temperatura a far letteralmente esplodere il combustibile. L’accensione è quindi istantanea e completa, ossia tutta la quantità di propellente esplode nello stesso istante, causando così un forte rumore. Oggi, grazie all’utilizzo dei motori multijet, si riescono a iniettare delle cariche di gasolio prima di quella principale; queste, iniziando ad accendersi in anticipo, svolgono la funzione della candela e fanno incendiare la carica principale in maniera graduale, con minor frastuono.
Il criterio inverso viene utilizzato nei moderni motori Diesel per abbassare le emissioni dannose e rigenerare i filtri antiparticolato. Nel primo caso, infatti, il problema è che il catalizzatore ha bisogno di elevate temperature per diventare efficiente, mentre i nuovi motori, avendo un alto rendimento, hanno temperature di scarico molto basse. Per questo si inietta una certa quantità di carburante dopo che è avvenuta la combustione principale, in modo che parte di quest’ultima accensione avvenga direttamente nei gas di scarico, che si scaldano prima dell’arrivo al catalizzatore. Nello stesso modo si rigenerano i nuovissimi filtri antiparticolato, disponibili di serie per poche autovetture di gamma alta e opzionali su alcune più piccole. Questi filtri “a trappola”, bloccano le particelle di particolato in una vera e propria gabbia. Per pulire il filtro servono elevatissime temperature, alle quali il particolato brucia e il sistema è rigenerato. Le soluzioni ad oggi adottate sono due: porre la gabbia subito a valle dei collettori e utilizzare il medesimo sistema del catalizzatore, o collocare il filtro a valle di quest’ultimo. In questo secondo caso, la carica viene erogata in forte ritardo rispetto all’accensione principale, in modo che il gasolio ancora incombusto passi attraverso i collettori e l’eventuale turbina e si incendi nel catalizzatore, dove le temperature sono elevate. Il controllo delle emissioni passa quindi attraverso quello che è chiamato il controllo sull’iniezione del carburante a ciclo chiuso (o closed loop): le quantità di combustibile e il momento in cui iniettare le cariche vengono stabilite in tempo reale (real time) sull’analisi dei dati provenienti da svariati sensori. I più comuni sono quelli relativi ai gas di scarico, come la temperatura all’uscita dai collettori o nel catalizzatore, ma oggi si riescono ad avere informazioni anche su quanto accade all’interno della camera di combustione, grazie a dei trasduttori di pressione montati direttamente sulle candelette.
I riparatori e la nuova “inaffidabilità” dei Diesel
Questo ingresso massiccio dell’elettronica ha migliorato le performance dei motori Diesel, sia da un punto di vista prestazionale sia da quello del comfort di marcia, a discapito però di una storica affidabilità. Il ciclo termodinamico su cui si basa il funzionamento rende questo tipo di motore praticamente inarrestabile. L’accensione della carica per compressione, infatti, garantisce il funzionamento in assenza completa di elettricità, rendendo il motore Diesel scevro da tutti i problemi di cui soffrono storicamente i concorrenti a benzina. Oggi però questi motori hanno un contenuto elettronico se possibile superiore a quello contenuto nei motori a ciclo Otto. Inevitabile, quindi, che le problematiche si siano trasferite in blocco sui propulsori a gasolio, con tutte le conseguenze che ciò comporta.
Se gli autoriparatori, in particolare, vedono crescere il numero di clienti rimasti in panne per problemi di elettronica, e per loro è sicuramente un dato positivo, la loro figura professionale sta man mano mutando con il passare degli anni. Oggi due figure professionali si stanno fondendo in un’unica attività: il vecchio meccanico è sempre più elettrauto e viceversa, con il risultato che ognuno deve essere in grado di risolvere problemi globali. Un’officina non dotata di un computer e degli strumenti di analisi e diagnosi elettronici è ormai automaticamente tagliata fuori del mercato.
Questa è una delle maggiori difficoltà che incontrano gli autoriparatori di una certa età, dove manca il ricambio generazionale. Se questa problematica è comune a tutti gli operatori del settore, per chi si occupa delle vetture Diesel è particolarmente gravosa. Le interconnessioni elettroniche in un motore a gasolio sono moltissime e vanno dalla gestione degli iniettori al controllo delle emissioni, tutte comunque passanti per la centralina, che ha il compito di gestire le informazioni. In queste condizioni è ovvio che, a farla da padrone in questo campo, siano i nuovi centri specializzati delle stesse Case e delle aziende che forniscono gli impianti di primo equipaggiamento. Il problema maggiore è quello di reperire le informazioni tecniche relative ai nuovi modelli e, in questo senso, la legge Monti (Ber) ha segnato una svolta; le Case, infatti, grazie alla nuova normativa sono obbligate a fornirle anche ai riparatori indipendenti. Queste, insieme agli aggiornamenti e ai corsi che vari produttori mettono loro a disposizione, garantiscono una qualità comparabile con quella offerta dalle Case, sia nella riparazione sia nella manutenzione. È in questi settori che si combatte, infatti, la battaglia più aspra e in quest’ottica le Case riteniamo possano solo perdere clientela, mentre ogni riparatore può accrescere il proprio pacchetto clienti offrendo servizi maggiori e prezzi più competitivi.
I nuovi prodotti e i distributori
Gli autoriparatori, tuttavia, per lavorare in maniera opportuna sulle auto dei loro clienti, hanno bisogno di essere continuamente riforniti con parti di ricambio, siano esse equivalenti o originali. È qui che entra in gioco la distribuzione: provvedere alle esigenze dei riparatori vuol dire essere sempre aggiornati, conoscere le nuove tendenze e offrire un magazzino comprendente i componenti di nuovi e vecchi veicoli. I motori Diesel, in tal proposito, rappresentano sicuramente un nuovo problema e al contempo una nuova possibilità.
La crescente diffusione di veicoli alimentati a gasolio ha fatto praticamente raddoppiare le scorte di magazzino che un distributore deve contabilizzare e gestire. Fino a un decennio fa, infatti, lo spazio dedicato al Diesel era molto inferiore a quello per le auto a benzina; oggi, con un parco circolante che tende alla parità, anche la composizione del magazzino deve essere adeguata. I ricambisti, inoltre, ultimo anello della catena che porta ricambi dai produttori alle officine, visto l’aumentare delle dimensioni del parco circolante e del numero di modelli di vetture disponibili sul mercato, tendono a non fare più magazzino, utilizzando la grande distribuzione in sua vece.
Per gestire un così vasto campionario di prodotti è sicuramente venuta in aiuto l’informatica: spariti i vecchi lucidi o gli obsoleti vetrini, oggi ogni magazzino conta su efficienti sistemi computerizzati di gestione delle scorte. La logistica integrata è il forte strumento su cui puntano attualmente le principali aziende di distribuzione, perché consente una combinazione più efficiente e razionale tra i settori dell’approvvigionamento. In questo senso, sicuramente aiutano le piattaforme di sviluppo comune utilizzate per la produzione dei veicoli. I grandi costruttori di automobili, infatti, non relizzano più un motore nella sua interezza, ma stabiliscono partnership con costruttori di componenti per lo sviluppo di particolari dei motori. Se questo è vero nel campo dei motori a ciclo Otto, ancora di più lo è per i moderni Diesel. Grandi gruppi multinazionali come Bosch, Delphi, Denso e Siemens hanno strette collaborazioni con le case auto, con il risultato che uno stesso prodotto è utilizzato su più modelli di motori fabbricati da aziende diverse. In termini di ricambi, ovviamente, questo vuol dire un numero minore di parti da trattare e una unificazione parziale degli strumenti di diagnostica necessari.
Le nuove tecnologie e i produttori
A beneficiare di questa unificazione sono anche i produttori di ricambi, anche se restare al passo con le tecnologie non è affatto semplice. Il mercato italiano dei produttori di ricambi Diesel è, in larga misura, diviso in due realtà sostanzialmente diverse: da una parte i grandi gruppi multinazionali, che svolgono ricerca e propongono sistemi completi con continue innovazioni, grazie ai progetti sviluppati in collaborazione con le case automobilistiche; dall’altra le realtà nazionali, specializzate perlopiù in singoli settori, le cui ali sono tarpate anche dagli inesistenti finanziamenti nazionali per la ricerca.
I problemi che i produttori si trovano continuamente ad affrontare nello sviluppo di ricambi Diesel sono legati sicuramente alla continua evoluzione di questo tipo di motori in ogni loro componente. Se i già citati sistemi di iniezione sono quelli maggiormente soggetti al fenomeno dell’innovazione e dell’”elettronicizzazione”, non da meno lo sono i nuovi materiali. I motori Diesel infatti, avendo un rapporto di compressione molto elevato, hanno bisogno di resistere a maggiori sollecitazioni. Ridurne il peso è uno di quegli obiettivi che la grande industria si è posta, anche in funzione del consumo di carburante. Così i costruttori meccanici classici, come quelli di componenti per il gruppo termico (pistoni, bielle, canne cilindro) si trovano a dover modificare i loro processi produttivi in funzione di ciò che il mercato offre (in particolare il largo impiego dell’alluminio). Il miglioramento delle performance è stato ottenuto anche attraverso il perfezionamento delle lavorazioni, il che si è tradotto in una riduzione delle tolleranze accettate e in una continua miniaturizzazione dei componenti.
Per i grandi marchi internazionali il discorso è ovviamente diverso: i sistemi Common Rail e iniettore pompa sono loro a svilupparli, proponendo sempre nuove soluzioni per il futuro e una esasperata ricerca delle prestazioni. Gli investimenti in ricerca di questi gruppi sono paragonabili a quelli che effettua uno stato e la stretta collaborazione con le Case garantisce il continuo miglioramento dei propri prodotti. Tuttavia, la legge Monti ha creato un nuovo e inedito conflitto di interessi: chi fornisce il primo equipaggiamento è ovviamente partner commerciale delle Case; come venditore Aftermarket è, invece, loro concorrente diretto. Se poi l’azienda ha pure una rete di ripazione affiliata, il conflitto è ancora più evidente.
Il Diesel del futuro
Lo sviluppo dei sistemi Diesel è comunque sicuramente una grande occasione, nonostante le problematiche che crea agli operatori del settore. Quando un mercato come quello dell’auto si ingrandisce, aumenta la richiesta di parti di ricambio e conseguentemente i margini di guadagno per tutti. Cerchiamo di capire allora in che direzione si muoveranno i grandi gruppi di ricerca nello sviluppo dei motori Diesel, tenendo sempre presente che fare previsioni a lungo termine è impossibile.
Nel breve periodo, invece, il nodo centrale attorno a cui si giocherà la partita più difficile è sicuramente legato all’ecologia. Le normative di tutto il mondo stanno imponendo vincoli sempre più restrittivi sulle emissioni di particolato e ossidi di azoto. Le Case si stanno attrezzano per rispondere ai requisiti richiesti con largo anticipo, studiando il modo per rendere i Diesel meno inquinanti.
Conseguenza diretta della realizzazione di motori più puliti sarà che consumeranno anche meno, con ovvio vantaggio dei consumatori finali. Per raggiungere tali risultati i gruppi di ricerca operano su più fronti e qualche anticipazione già trapela. Lo sviluppo di nuove pompe porterà la pressione dei Common Rail dagli attuali 1.600 bar ai 1.800 bar previsti per il 2005 e consentirà di superare la soglia dei 2.000 nell’anno successivo; per il 2007 è attesa invece la quarta generazione di questi sistemi, che dovrebbe avere come caratteristica una pressione di oltre 2.200 bar.
Altra novità che si è già vista su qualche nuovo motore, ma che è al centro di studi per futuri sviluppi, sono gli iniettori piezoelettronici in linea (nel caso di Bosch) o ad attuazione diretta (Delphi). La caratteristica di questi sistemi è quella di abbattere in modo sostanziale i tempi tra le iniezioni, fornendo ai progettisti di motori la libertà di modulare il flusso di carburante durante tutto il ciclo di combustione, assicurando tempi di attuazione estremamente ridotti. Sugli iniettori la ricerca è comunque a 360 gradi e così si studiano anche sistemi con polverizzatori a geometria variabile, che consentiranno una iniezione ancora più modulabile e precisa.
Il sistema alternativo al Common Rail, invece, ovvero l’iniettore pompa (o Unit Injector System), sviluppato da Bosch in esclusiva per Volkswagen, è attualmente il meccanismo che consente la massima pressione per i motori Diesel, con 2.050 bar e già dal prossimo anno avrà ulteriori step evolutivi.
La vera novità potrebbe essere la combinazione dei due sistemi, come è stato ventilato durante l’ultimo salone del veicolo industriale di Hannover, ossia il raggiungimento di una pressione di circa 1.000 bar nel Rail (o serbatoio comune) e una ulteriore pressurizzazione fino a 2.500 bar direttamente nell’iniettore. Si tratta ancora di studi, perlopiù destinati solo ai veicoli commerciali, ma non bisogna dimenticare che proprio da questi sono arrivate molte novità tecnologiche, come il Turbo. È stato proprio quest’ultimo, infatti, il meccanismo che per primo ha dato impulso al rilancio del Diesel: montato sulle prime Volvo Turbodiesel, i cui motori erano, appunto, quelli di veicoli commerciali riadattati.
L’ultima novità tecnica di rilievo in questo settore è stata l’introduzione delle turbine a geometria variabile negli impianti di sovralimentazione, che sopperiva in modo parziale al problema di incompatibilità tra il ritardo della turbina ai bassi regimi e la disponibilità di grandi riserve di potenza agli alti. L’evoluzione di questo sistema è oggi montato sulla nuova BMW 535d e sfrutta una tecnologia già utilizzata negli impieghi marini e sui veicoli industriali leggeri: la turbina multistadio. Dopo aver compresso l’aria di aspirazione nella prima piccola turbina l’aria viene inviata alla seconda, più grande, dove viene ulteriormente compressa. L’aria attraversa quindi un intercooler per giungere al momento dell’immissione nella camera di combustione a una pressione massima di 2,85 bar.