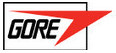
Il numero di componenti elettronici nei veicoli sta aumentando in modo esponenziale, sia per la crescente elettrificazione dei componenti meccanici, sia per l'uso sempre più esteso dei sistemi di assistenza alla guida. Aumenta così la difficoltà per le case automobilistiche e i loro fornitori nel proteggere l'elettronica. Infatti, per motivi di costo, ma anche per posizionare il proprio marchio tra quelli più affidabili e prestigiosi, i componenti elettronici devono funzionare in modo sicuro per l'intera vita di un'auto. L'azienda GORE ci spiega come le soluzioni a membrana proteggono efficacemente l'elettronica dalla sporcizia e dai guasti.
Che si tratti di compressori, pompe, motori o centraline, i componenti elettronici sono esposti a forti escursioni termiche, che possono causare sovrappressioni o depressioni elevate negli involucri elettronici. Queste sollecitano le guarnizioni e gli elementi sigillanti, fino a far penetrare particelle di sporcizia o liquidi all'interno dei componenti elettronici, corrodendoli.
La sfida: l'elettronica e le batterie nei veicoli elettrici
La gestione termica dell'elettronica e delle batterie nei veicoli elettrici è una delle maggiori sfide, perché questi componenti raggiungono le massime prestazioni soltanto a determinate temperature. Spesso si surriscaldano ed è necessario raffreddarli a liquido. Ma le differenze di temperatura all'interno sono tali da risultare nella formazione di condensa, causando corrosione o cortocircuiti. Nelle grandi batterie questa problematica raggiunge proporzioni critiche. Bastano differenze minime di temperatura per generare una pressione sull’involucro e deformarlo. D'inverno può formarsi un vuoto che esercita una pressione di 500 kg per metro quadrato, a cui un involucro leggero non può resistere.
Tecnologia a membrana: garantire l’equalizzazione dell'aria e della pressione
Gli OEM ora hanno tre possibilità: primo, sigillare i componenti elettronici negli involucri, ottenendo un sistema stagno, ma più pesante e non riparabile. Secondo, creare sistemi ermetici utilizzando guarnizioni di alta qualità e involucri con pareti più spesse, a discapito dei costi e del peso. Risulta invece più efficace una terza soluzione: utilizzare una membrana che equalizza la pressione dell’aria all'interno dell’involucro chiuso e, al contempo, impedisce la penetrazione di liquidi e sporcizia.
La grafica mostra come il vuoto aumenta progressivamente all'interno di un involucro stagno. Negli involucri non sfiatati sono sufficienti 7 kPa di pressione per provocare la perdita di tenuta delle guarnizioni. Gli involucri sfiatati equalizzano la pressione e prevengono le perdite.
Curve caratteristiche importanti: flusso d'aria e pressione d'ingresso dell'acqua
Il flusso d'aria (Airflow) e la pressione d’ingresso dell'acqua (Water Entry Pressure) sono le due caratteristiche che determinano le proprietà di una membrana. Il flusso d'aria indica quanta aria attraversa la membrana in un determinato tempo e a una determinata variazione di pressione, definendo il tempo in cui è possibile equalizzarla. La pressione d’ingresso dell'acqua è la pressione idrostatica minima alla quale la membrana deve resistere. Entrambi dipendono anche dalla porosità della membrana. Il compito di ogni fornitore è trovare l'equilibrio perfetto tra Airflow e Water Entry Pressure.
I componenti elettronici però tendono a diventare sempre più piccoli, costringendo i costruttori a ridimensionare anche i sistemi di sfiato, il che richiede un flusso d'aria maggiore in relazione alla superficie della membrana e, di conseguenza, una pressione d'ingresso più bassa.
Per definire il grado di ermeticità di un sistema si utilizzano le classi di protezione IP (secondo la norma DIN 40050-9), che definiscono il livello di protezione dell’involucro nei confronti dell’ingresso di solidi o di liquidi. La prima cifra indica la classe di protezione rispetto ai solidi, la seconda si riferisce alla protezione dai liquidi. La classe IPX9K indica il livello di protezione dell’involucro, compresa la membrana, rispetto alla penetrazione di acqua proveniente da un getto vaporizzato ad alta pressione.
Nel test l’involucro e la membrana integrata vengono colpiti da un getto vaporizzato a una distanza compresa tra 100 e 150 mm, con un'angolazione di 0, 30, 60 e 90 gradi. Il flusso volumetrico varia tra 14 e 16 l/min, la pressione dell'acqua tra 8.000 e 10.000 kPa e la temperatura è di 80°C.
Resistenza ai prodotti chimici di una membrana ePTFE
Gore utilizza il PTFE (politetrafluoroetilene), caratterizzato da una microstruttura inconfondibile, ideale per applicazioni di sfiato. Il PTFE viene espanso per creare una membrana a micropori in cui i nodi sono collegati tra loro da sottili fibre, ottenendo così il "politetrafluoroetilene espanso" (ePTFE), eccezionalmente idrorepellente e oleorepellente. Questo è essenziale nel settore automobilistico, perché è molto probabile il contatto con olio motore, detergenti e altri liquidi.
Gore sperimenta la resistenza delle proprie applicazioni di sfiato nei confronti di oltre 20 diverse sostanze chimiche (in conformità con ISO 16750-5). Le membrane vengono messe a contatto con il liquido e lasciate a temperatura ambiente (da 21 a 23°C) per 24 ore, oppure riscaldate per 96 ore in forno. Prima e dopo il test vengono misurati il flusso d'aria e la pressione d'ingresso dell'acqua.
Al di sotto della linea nera la membrana viene compromessa. La membrana in questo esempio è adatta a essere bagnata con conservanti (o deceranti) soltanto entro certi limiti, mentre per tutte le altre sostanze chimiche soddisfa le specifiche richieste.
Termostabilità dell'ePTFE
Un altro vantaggio dell'ePTFE è la resistenza alle temperature da -150°C a +240°C. Una caratteristica utile nei vani motore, in cui oggi spesso si superano i 125°C per i quali finora erano stati concepiti gli involucri elettronici.
Gore collauda la resistenza delle proprie Vent (ISO 16750-4) in primo luogo tramite il "Temperature Resistance Test", esponendo il sistema per 2.000 ore a una temperatura massima di 150°C e per 1.000 ore a -40°C. La seconda prova è l’"Ice Dunk Test": in un contenitore ermetico la Vent viene riscaldata per 40-60 minuti a 80-125°C. Infine l’involucro viene immerso in acqua ghiacciata, contenente il 5% di cloruro di sodio, e raffreddato a 0-4°C, simulando le condizioni invernali. La procedura viene ripetuta fino a 20 volte, misurando le caratteristiche di sfiato prima e dopo il test.
Soluzioni con membrane in diverse configurazioni
È decisivo scegliere la membrana migliore per la propria personalizzazione. Gore propone sistemi di sfiato autoadesivi e saldabili, oltre a componenti integrati in supporti plastici. Le membrane autoadesive di Gore sono dotate di un adesivo attivato dalla pressione, con un elevato grado di aderenza; vengono fornite su un supporto a bassa adesione (per facilitarne la manipolazione) e possono essere applicate sia manualmente, sia a macchina. Il collante è a lunga durata e alta resistenza, in ogni caso è principalmente destinato a componenti che hanno un contatto non intensivo con sostanze chimiche.
I dischi di protezione e sfiato da saldare sono prodotti in diversi materiali e dimensioni. Si utilizzano quando l’involucro è plastico, ed è il cliente a effettuare la saldatura a ultrasuoni, che garantisce un'aderenza ermetica e duratura. Poiché il punto di fusione del PTFE supera abbondantemente la sua temperatura di saldatura, la membrana non viene compromessa. I sistemi di sfiato rappresentano una soluzione durevole e affidabile anche in presenza di temperature elevate e sostanze chimiche aggressive. Il processo di saldatura però è molto complesso e richiede personale qualificato. Per proteggere l'elemento dai getti di vapore e dalle sollecitazioni meccaniche inoltre si devono integrare pareti protettive nell’involucro.
Una soluzione resistente e semplice sono i componenti integrati in materiale plastico, i Molded Parts. La procedura di costampaggio di Gore, ad esempio, integra la membrana nel processo di stampaggio a iniezione. I componenti in questo modo possono essere inseriti a scatto nell'involucro. La membrana è protetta da sollecitazioni meccaniche senza dover integrare altri accorgimenti protettivi complicati e costosi. Non sono necessari macchinari speciali né personale qualificato, perché la Vent si utilizza "plug&play".
Promessa di qualità: la soluzione di sfiato personalizzata
Per soddisfare le specifiche dell'applicazione e superare i test richiesti, fin dalle prime fasi Gore viene coinvolta nello sviluppo del prodotto del cliente. Dopo aver definito tutti i requisiti, Gore sceglie dal proprio portfolio il prodotto adatto oppure sviluppa una soluzione specifica e personalizzata in collaborazione con gli OEM e i fornitori delle case automobilistiche, non soltanto soddisfacendo gli standard attuali, ma tenendo anche già conto delle esigenze del futuro.